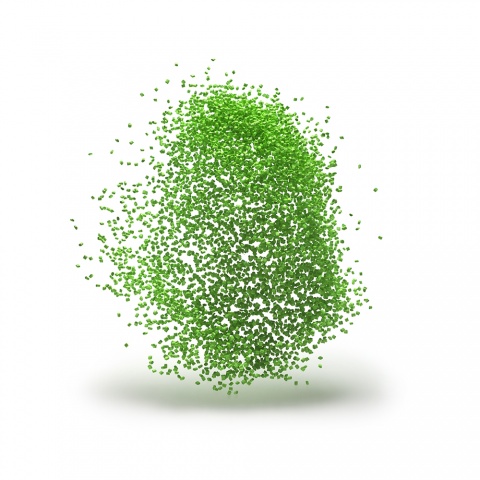
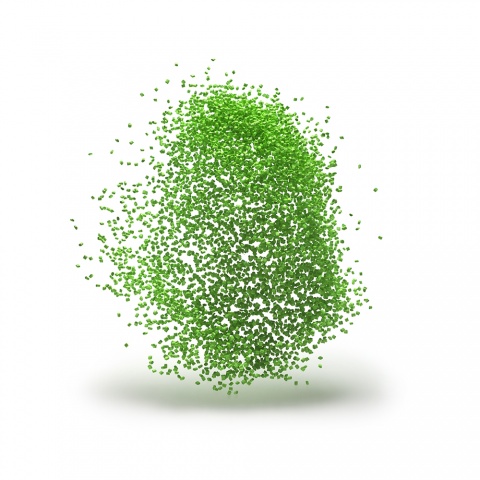
Fluoropolymer
Increasingly more technical applications in aggressive environments, in terms of temperature, chemical agents and atmospheric conditions, made it possible for fluoropolymers to find more space on the market. These polymers offer extremely high performance, though at elevated costs regarding both raw materials and production. Depending on the bond between carbon and fluorine, and their arrangement in the molecular structure, one can have varying products with different characteristics. Concerning chemical resistance and use at low and high temperatures, the father of all fluoropolymers is PTFE, which demonstrates almost complete inertia towards most known chemical reagents and has work temperatures that range from -260 to +260 °C. After PTFE, these other fluoropolymers can be found, in order of importance: PFA, FEP, and PVDF.
HISTORY
On April 6th, 1938 in the laboratories of Kinetic Chemicals, a company created from the partnership of DuPont and General Motors, Roy J. Plunket was doing some experiments with tetrafluoroethylene gas when he chanced upon an anomaly: the previously pressurized gas had disappeared from the cylinders; in fact, the pressure gauge on these cylinders read zero. After taking apart the cylinder, he gathered a solid white mass that had the same weight of the gas that had been pressurized; this particularly slippery substance was the first form of polytetrafluoroethylene to be synthesized, probably from the reaction of the gas with iron. The first experiments immediately demonstrated the exceptional properties of this polymer. In 1941 DuPont patented polytetrafluoroethylene (PTFE), and three years later, in 1945, they launched the commercial brand Teflon, the name that by now encompasses all of the fluoropolymers. This polymer, practically resistant to attack from all chemical agents and microorganisms, has a slippery consistency with anti-adhesion (non-stick) properties to almost all glues and paints and offers optimal mechanics both at low and elevated temperatures. However, it was hiding a significant problem: it is unable to flow in the molten state, and consequentially cannot be processed using the normal technologies established for thermoplastic polymers. The engineers at DuPont that were able to process it, did so by borrowing technologies from the metallurgy of powders and producing tubes for transporting the fluids. The objective difficulties of production, however, necessitated the development of a fluoropolymer that was able to combine the properties of PTFE with commonly used technologies.
Thus, in 1960, DuPont introduced Teflon™ FEP (fluorinated ethylene propylene), the first fluoropolymer that could be processed in the molten state. The family of fluoropolymers was still missing a product that combined elevated chemical resistance and elevated mechanical properties with simplicity of production, which was crucial given FEP’s high temperatures of transformation (above 280°C). This request was satisfied by Polyvinylidene Fluoride, PVDF, patented in 1948 but set aside until the 1960s: the first commercial production of this polymer, introduced to the market with the brand KYNAR, started in 1965 and it immediately proved to have elevated mechanics and the ability to transform at temperatures of around 220°C. In 1970 DuPont introduced Tefzel™ ETFE, a modified copolymer of ethylene and tetrafluoroethylene, that satisfied the requirements of elevated mechanical properties at elevated temperatures. ETFE is particularly suitable for wire coverings and for insulation that is resistant to 155°C for 20,000 hours of continuous exposure. In 1972, DuPont introduced Teflon ™ PFA (perfluoroalkoxy, a copolymer of tetrafluoroethylene and perfluoroalkyl vinyl ether) whose properties meet halfway between those of PTFE and FEP. The studies on PVDF continued and in 1984 a new series of homopolymers, called KYNAR FLEX® 2800, was introduced, thus supplying the market with a soft variant of this polymer.
MORPHOLOGY
All fluoropolymers are semi-crystalline polymers but vary in their opacity. PTFE and PVDF are both opaque, while PFA and FEP are completely transparent.
STRUCTURE
The fundamental structures for all fluoropolymers are a combination of carbon and fluorine atoms that are repeated equally along the whole length of the chain. Based on this arrangement, the properties can vary enormously.
COMPARISON
Increasingly more technical applications in aggressive environments, in terms of temperature, chemical agents and atmospheric conditions, made it possible for fluoropolymers to find more space on the market. These polymers offer extremely high performance, though at elevated costs regarding both raw materials and production. Depending on the bond between carbon and fluorine, and their arrangement in the molecular structure, one can have varying products with different characteristics. Concerning chemical resistance and use at low and high temperatures, the father of all fluoropolymers is PTFE, which demonstrates almost complete inertia towards most known chemical reagents and has work temperatures that range from -260 to +260 °C. After PTFE, these other fluoropolymers can be found, in order of importance: PFA, FEP, and PVDF.
THE FOLLOWING DIFFERENCES CAN BE OBSERVED
PFA offers consistent performance over continuous use in the same range of temperatures as PTFE, thus matching one of the dominating characteristics of the latter. The continuous working temperatures of FEP and PVDF are lower: that of FEP is 200 °C and that of PVDF is 100°C. PTFE has a viscosity in the molten state that does not allow it to be used with the conventional technologies. The viscosities of PFA, FEP, and PVDF, however, are more than one million times less than PTFE’s, thus allowing their processing with the technologies put in place for thermoplastic resins (extrusion, molding, etc.). Among these, PVDF stands out for its ease of processing, due in part to its melting point of 145-170°C, compared to 260°C for FEP and 305°C for PFA. PFA is similar to FEP in many aspects (transparency, chemical resistance, etc.), but in general has better mechanical properties at higher temperatures. PTFE, for its part, is similar to PFA, but at elevated temperatures, above 120°C, is better able to maintain its mechanical characteristics. Regarding flex-life and stress-cracking resistance, PFA is superior to FEP, which is, in turn, superior to PTFE. This classify first two products as a preferential choice in case of applications that in addition to exposing the product to chemical agents exposes it to mechanical stress. Generally, however, FEP has lower tensile strength and creep than PFA and PTFE. Conversely, PDVF, in its range of service temperatures, shows better mechanical performance both when high rigidity is required (with modulus that reach 2300 Mpa, compared to PTFE’s that do not go beyond 750Mpa) and when flexibility is required. PTFE, FEP, PFA, and PVDF are intrinsically self-extinguishing (UL94 V0), with LOI (index meaning the minimum quantity of oxygen necessary in the atmosphere to sustain flames) >95% for PTFE, FEP, and PFA and >40% for PVDF. PTFE, FEP, and PFA exhibit the same resistance to atmospheric agents, solar light, and oxidizing agents. Test samples that were exposed for many years in nearly all climatic conditions did not show either visual ageing or embrittlement. PVDF exhibits exceptional thermal stability. For example, in experiments of continual exposure to 150°C over a period of 10 years it did not show any oxidative effect or thermic degradation.
Fluoropolymer
Increasingly more technical applications in aggressive environments, in terms of temperature, chemical agents and atmospheric conditions, made it possible for fluoropolymers to find more space on the market. These polymers offer extremely high performance, though at elevated costs regarding both raw materials and production. Depending on the bond between carbon and fluorine, and their arrangement in the molecular structure, one can have varying products with different characteristics. Concerning chemical resistance and use at low and high temperatures, the father of all fluoropolymers is PTFE, which demonstrates almost complete inertia towards most known chemical reagents and has work temperatures that range from -260 to +260 °C. After PTFE, these other fluoropolymers can be found, in order of importance: PFA, FEP, and PVDF.
PVDF
PVDF is a semi-crystalline polymer obtained from the…
PTFE
PTFE is a fluoropolymer with high molecular weight, comprised of only of carbon…
FEP
FEP exhibits exceptional thermal properties, electrical properties, and chemical…
PFA
PFA is a completely fluorinated copolymer that has small branches, which vary…
Featured products
You might also be interested in
There are four macro polymers that we work with to produce our tubes. Polyamides and polyurethanes are the most common solution for automation and therefore the passage of compressed air. When the tube comes to contact with fluids other than air or is installed in harsh environment conditions, fluoropolymer tubes intervene. When the cheapest solution is the key, polyethylenes have the upper hand.
Polyamide
The success of polyamides is due to a combination of characteristics that make them ideal for many applications. Polyamides combine optimal mechanical properties with excellent chemical resistance; they can be used as metal substitutes or even as elastomers; they can be used in both protected and ag...
Polyurethane
The term polyurethane encompasses a vast family of products with numerous varied characteristics in terms of mechanical, chemical and physical properties. Through the right choice and proportion of polyols and diisocyanates it is possible for products to range from soft and sponge-like, such as flex...
Polyethylene
Polyethylene, making up 40% of the total volume of plastic materials produced in the world, is one of the most diffused polymers in everyday life. Despite its simple chemical composition, there are numerous varieties of polyethylene with differing thermal and mechanical properties.
Other products
To complete the range, we offer PVC and silicone pipes and various accessories for cutting, organizing and protecting our products.