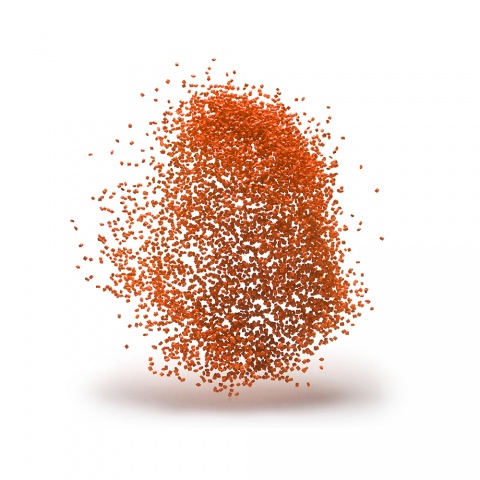
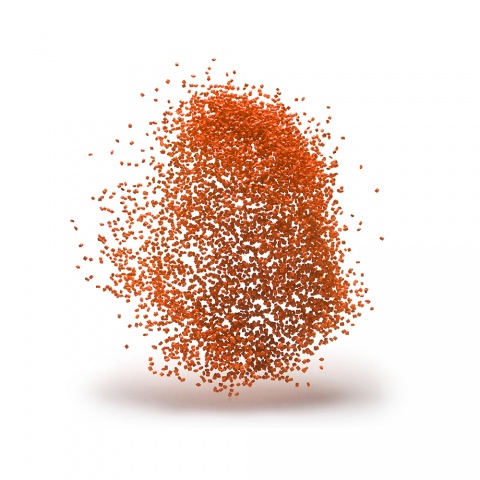
Polyurethane
The term polyurethane encompasses a vast family of products with numerous varied characteristics in terms of mechanical, chemical and physical properties. Through the right choice and proportion of polyols and diisocyanates it is possible for products to range from soft and sponge-like, such as flexible foams with extremely low density (pillows, mattresses, etc.) to products with elevated resistance to compression and flexion stress (for applications in sporting goods, such as hiking boots, ski boots, etc.). In order to have a general guide regarding the characteristics of polyurethane, the primary distinctions to consider relate to its chemical nature, or rather, if it has an ester or ether base. In commerce there is also a third family of polyurethane, which derives from the synthesis of caprolactam, which exhibits intermediate characteristics between polyester and polyether.
HISTORY
The synthesis of the first aliphatic isocyanate occurred in the mid-19th century following some experiments done by Adolfo Wűrtz. Successively, in 1937, Otto Bayer, a doctor working in the Bayer laboratories in Germany, polymerized a polyurethane through the polyaddition of poly-isocyanates (also known as diisocyanates) and polyols. He was aiming to obtain a fiber product that could be similar to nylon from the United States, but that was free from blocking patents. The controlled synthesis and commercialization of these new fibers, however, had to wait until 1964, when the Bayer laboratories introduced it to the market under the brand Dorlastan®. In common jargon today, this polyurethane fiber, which is used for a multitude of clothing articles, is associated with the name Lycra®. This name was given to it by Du Pont, which actually introduced it to the market in 1960, 4 years before its adversary, Bayer. Thus, it became known as Lycra®.
Previously (starting from 1945), the chemistry of polyurethane had only allowed it to be used for elastomers, coatings, and adhesives. The first polymerizations were developed with ester polyols and only after about 10 years ether polyols were introduced to the market, thus creating two types of polymers, with different characteristics, in the same polyurethane family. From the early 1960s, the polyurethane market experienced considerable growth. This was initially due to the introduction of flexible foams but was also later due to the introduction of rigid foams, which appeared after about 10 years. The continued improvements in its synthesis, still in development today, as well as the introduction of new transformation technologies have caused polyurethane to be used in practically all fields of application: flexible hoses, wheels, thermal and acoustic insulation, belts, gaskets and seals, cables, shoe soles, ski boots, adhesives, etc
MORPHOLOGY
The complexity of the synthesis methods, regarding the monomer base structures, the interaction between monomers, and the many types of catalysts and additives used make it possible to achieve a product with different qualities. For example, the obtained polymer can vary from semi-crystalline and opaque to amorphous and transparent, and its structure can range from textile fibers to soft expansive foam.
STRUCTURE
The synthesis of polyurethane (PU) can be summarized by the chemical reaction of diisocyanates, molecules containing two or more -N=C=O groups, with polyols (generally diols), molecules containing two or more hydroxyl groups -OH. The polyols have long chains and the diols have short chains. From the diol emerges the distinction between the ester-based polyurethane (R-C=OO-R’) and the ether-based polyurethane (R-O-R’).
COMPARISON
The term polyurethane encompasses a vast family of products with numerous varied characteristics in terms of mechanical, chemical and physical properties. Through the right choice and proportion of polyols and diisocyanates it is possible for products to range from soft and sponge-like, such as flexible foams with extremely low density (pillows, mattresses, etc.) to products with elevated resistance to compression and flexion stress (for applications in sporting goods, such as hiking boots, ski boots, etc.). In order to have a general guide regarding the characteristics of polyurethane, the primary distinctions to consider relate to its chemical nature, or rather, if it has an ester or ether base. In commerce there is also a third family of polyurethane, which derives from the synthesis of caprolactam, which exhibits intermediate characteristics between polyester and polyether.
The macro differences between ester polyurethane and ether polyurethane are:
The ester-based polyurethane exhibits better mechanical characteristics from practically all points of view: elastic modulus, resistance to traction, tears, compression, abrasion, static traction tests, etc. However, there is an exception when considering its flexibility in the cold and its resistance to impact at low temperatures; in these conditions the “ether” performs better. Even considering the mechanical characteristics at room temperature and the aging at high temperatures, the ester-based polyurethane behaves better. The situation is reversed when considering the resistance to hydrolysis and to the attack of microorganisms. The phenomenon of hydrolysis, which literally means “division produced by water,” affects the “ester” significantly, leading to depolymerization, thus to a reduction in molecular weight with a resulting loss of mechanical properties; this phenomenon is more significant in soft polyurethanes in which the polyol has greater numbers of ester groups. Similarly, in high temperature and humidity conditions, the ester polyurethane is sensitive to enzymatic attack by bacteria and fungi that provoke the division of the ester bond, which leads to a reduction of mechanical characteristics. Both types of polyurethanes show resistance to oils, greases, oxygen and ozone, but the ester-based polyurethane also offers better impermeability to gases (Ar, CO2, N2,O2, etc.). The last point to consider, but not the least important, regards density. The ether-based polyurethane proves to be lighter, and thus has a lower density, which results in related advantages in the transportation sector and in all applications with high amounts of movement.
Summarizing the principle differences, the ester-based polyurethane proves to have:
-
better mechanical behavior at room temperature
-
better behavior at high temperatures
-
better barrier effect to gases
The ether-based polyurethane has, instead:
-
better resistance to hydrolysis
-
better flexibility and impact resistance at low temperatures
-
better resistance to microorganisms
-
lower weight
Polyurethane
The term polyurethane encompasses a vast family of products with numerous varied characteristics in terms of mechanical, chemical and physical properties. Through the right choice and proportion of polyols and diisocyanates it is possible for products to range from soft and sponge-like, such as flexible foams with extremely low density (pillows, mattresses, etc.) to products with elevated resistance to compression and flexion stress (for applications in sporting goods, such as hiking boots, ski boots, etc.). In order to have a general guide regarding the characteristics of polyurethane, the primary distinctions to consider relate to its chemical nature, or rather, if it has an ester or ether base. In commerce there is also a third family of polyurethane, which derives from the synthesis of caprolactam, which exhibits intermediate characteristics between polyester and polyether.
Featured products
You might also be interested in
There are four macro polymers that we work with to produce our tubes. Polyamides and polyurethanes are the most common solution for automation and therefore the passage of compressed air. When the tube comes to contact with fluids other than air or is installed in harsh environment conditions, fluoropolymer tubes intervene. When the cheapest solution is the key, polyethylenes have the upper hand.
Polyamide
The success of polyamides is due to a combination of characteristics that make them ideal for many applications. Polyamides combine optimal mechanical properties with excellent chemical resistance; they can be used as metal substitutes or even as elastomers; they can be used in both protected and ag...
Fluoropolymer
Increasingly more technical applications in aggressive environments, in terms of temperature, chemical agents and atmospheric conditions, made it possible for fluoropolymers to find more space on the market. These polymers offer extremely high performance, though at elevated costs regarding both raw...
Polyethylene
Polyethylene, making up 40% of the total volume of plastic materials produced in the world, is one of the most diffused polymers in everyday life. Despite its simple chemical composition, there are numerous varieties of polyethylene with differing thermal and mechanical properties.
Other products
To complete the range, we offer PVC and silicone pipes and various accessories for cutting, organizing and protecting our products.