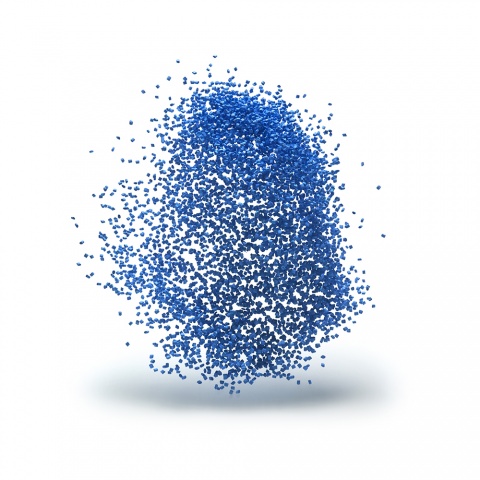
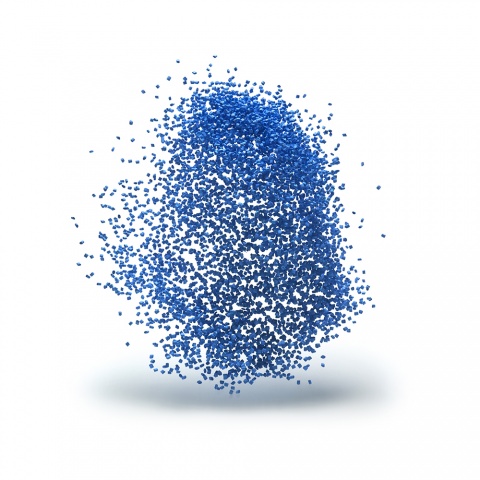
Polyethylene
Polyethylene, making up 40% of the total volume of plastic materials produced in the world, is one of the most diffused polymers in everyday life. Despite its simple chemical composition, there are numerous varieties of polyethylene with differing thermal and mechanical properties.
HISTORY
The first documented traces of the synthesis of Polyethylene date back to 1898 to the work of German chemist, Hans Von Pechmann. It started with diazomethane, whose original conditions of synthesis were unable to be reproduced. In March 1933, Eric Fawcett and Reginald Gibson, two chemists in the English laboratories of the ICI, Imperial Chemical Industries, did a night-time experiment with ethylene gas at extremely high pressure, which resulted in the discovery of a waxy layer in the bottom of the autoclave. In 1936 Michael Willcox Perrin patented the synthesis of polyethylene and, in 1939, the first industrial production of what we can easily identify with the acronym LDPE (Low Density Polyethylene) began. The first tests showed its exceptional insulation properties and it was immediately used as a substitute for gutta percha, to insulate electrical cables in submarines. During World War II, polyethylene became a “top secret” material in that they discovered its efficient shielding properties at high frequencies. This shielding capacity, in combination with its lightness, caused polyethylene to become the essential product for radar use on airplanes, which required these very two characteristics.
In 1951, two chemists at the Phillips Petroleum Company, John P. Hogan and Robert L. Banks, were able to produce, with the use of specific catalysts, a polyethylene that was much more resistant: HDPE (High Density Polyethylene). The Phillipstype catalyst showed irregular results with large production quantities of polyethylene, whose characteristics were inconsistent and outside of specifications. In 1954, during one of his experiments with ethylene, Karl Ziegler, a German chemist and the director of the Max Planck Institute in Mülheim, Germany, made an accidental discovery. Due to the erred cleaning of the reactor, which was left dirty with nickel salts, Ziegler’s experiment resulted in the synthesis of a dimer of ethylene; this accident led him to a systemic analysis of all of the metallic salts. He was thus able to find the combination that would allow for the production of polyethylene with a regular linear structure, high molecular weight, and consistent reproducible characteristics. In 1980, with the progress of catalyst technology, a linear polyethylene with low density was achieved (LLDPE, Low Linear Density Polyethylene); LLDPE is an intermediate between HDPE and LDPE.
MORPHOLOGY
Polyethylene, whether LDPE, LLDPE, or HDPE, has a semi-crystalline form with a percentage that can vary from 40 to 80% depending on the grade of polyethylene.
STRUCTURE
The base monomer, the unit that is repeated identically along the whole length of the chain, is the same for all types of polyethylene.
What distinguishes LDPE, LLDPE, and HDPE from a structural point of view is the quantity and type of branching, as seen in the schematic diagram below.
COMPARISON
Polyethylene, making up 40% of the total volume of plastic materials produced in the world, is one of the most diffused polymers in everyday life. Despite its simple chemical composition, there are numerous varieties of polyethylene with differing thermal and mechanical properties. These properties vary based on the molecular structure of the chains that make up the polyethylene and determine its type of use. As can be inferred from the name, the Density determines the distinction between the macro categories. This intensive property of the semi-crystalline polymers depends on their crystallinity, meaning the fraction of the polymer that is arranged in an orderly way and occupies the least possible volume. Conversely, the amorphous part is due to the introduction of branching in the principle chain, as seen in the above image, that impedes the correct organization of crystals in the polymer, and consequently, indicates a reduction in density. The crystalline structure dictates many properties of the polymer, such as its optical properties, melting and softening points, elastic modulus, yield strength, etc. The greatest differences between LDPE, LLDPE, and HDPE are those related to their mechanical properties. HDPE is always more resistant to traction and flexion, and is harder and more opaque than LLDPE which, in turn, is better-performing than LDPE. The higher melting temperatures of HDPE make it suitable for applications that are near heat sources. Even the gas and vapor barrier properties follow the same trend as the mechanical properties: HDPE remains the best, followed by LLDPE and lastly LDPE.
A clarification has to be made between LDPE and LLDPE:
The two polymers can exhibit the same density and melting point but LLDPE shows better mechanical characteristics, due to the presence of small branches (in LLDPE; maximum 6 units) in the principle macromolecule. These branches, being linear, justify the equivalence of the density values as well as LLDPE’s superior mechanical properties. Regarding the resistance to atmospheric agents, all three families experience damage from ultraviolet rays, with resulting deterioration of physical characteristics. Regarding resistance to chemical attacks, LLDPE and HDPE perform better than LDPE. LDPE, instead, is the most economical of all the types of polyethylene.
Polyethylene
Polyethylene, making up 40% of the total volume of plastic materials produced in the world, is one of the most diffused polymers in everyday life. Despite its simple chemical composition, there are numerous varieties of polyethylene with differing thermal and mechanical properties.
Featured products
You might also be interested in
There are four macro polymers that we work with to produce our tubes. Polyamides and polyurethanes are the most common solution for automation and therefore the passage of compressed air. When the tube comes to contact with fluids other than air or is installed in harsh environment conditions, fluoropolymer tubes intervene. When the cheapest solution is the key, polyethylenes have the upper hand.
Polyamide
The success of polyamides is due to a combination of characteristics that make them ideal for many applications. Polyamides combine optimal mechanical properties with excellent chemical resistance; they can be used as metal substitutes or even as elastomers; they can be used in both protected and ag...
Polyurethane
The term polyurethane encompasses a vast family of products with numerous varied characteristics in terms of mechanical, chemical and physical properties. Through the right choice and proportion of polyols and diisocyanates it is possible for products to range from soft and sponge-like, such as flex...
Fluoropolymer
Increasingly more technical applications in aggressive environments, in terms of temperature, chemical agents and atmospheric conditions, made it possible for fluoropolymers to find more space on the market. These polymers offer extremely high performance, though at elevated costs regarding both raw...
Other products
To complete the range, we offer PVC and silicone pipes and various accessories for cutting, organizing and protecting our products.